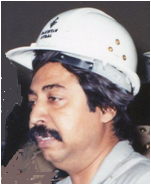

Factors confine the productivity
of LD-Converter (Steel Making
Department Pakistan Steel).
With the recent setting up of new ore
based (BF- Converter route) integrated steel plants in China, India and Brazil
along their coastal areas, the share of Converter steelmaking has stabilized
and maintained at 70% of the world’s total steel production.
The LD-Converter is the key component
in the steel production process in an integrated steel plant like Pakistan
Steel. The productivity of a steel plant is dependent to a large extent on the
availability of the Converter (BOF) for production.
A view of working platform of 130 ton LD-Converter(Elevation + 8 meter).
Steel Making Department of Pakistan
steel is comprised of two 130 Tons LD-Converters (one in operation
and second as standby) to achieve the Phase - I production of 1.1
million tons per year. Whereas the foundations for installing third 130 ton
LD-Converter were made available in the steel making department as per project
to enhance the Phase - II production to 2.2
million tons per year.
Tap to Tap Cycle of LD-Converter.
After every 40 - 55 minutes, a batch of molten
steel (called a heat ) is tapped from LD-Converter into a Steel
ladle known as tap-to-tap
cycle. Steel tapping cycle is matched/ synchronized with the speed of
particular continuous casting machine in operation ( Billet, Bloom or Slab
caster).
The
cyclic steps of LD-Converter operation:
Heat
cycle may be interrupted due to :
-
late
arrival of ladle from Ladle preparation section;
-
prolonged
gunning repair;
-
prolonged
Converter’s mouth cleaning operation;
-
unforeseen
automation/ electrical/ mechanical fault cropped up in any process instrument
or equipment;
-
any
re-blow for correction of chemistry/ temperature when the Converter
melting shop is working without having
computer controlled dynamic process model (may have a separate discussion) and Ladle
Furnace facility.
After tapping a heat from
Converter, the steel ladle is dispatched via an electrically driven ladle car
to Continuous casting bay where a 180 ton over head crane transports it to ladle
treatment station and then onward to the scheduled Continuous Caster ( Billet,
Bloom or Slab),
In
modern high productivity Steel making shops, Converter’s tap-to-tap cycle of a
heat is typically designed closest to 35 minutes by carrying out fine-tuning of molten
steel at ladle treatment station, facilitated with Ladle Furnace and
Vacuum-degasser.
At
present the most common worldwide de-oxidation and alloying practice is a split
practice. The major part of de-oxidation
and alloys addition is carried out during steel tapping from converter where as
fine tuning of chemical composition and temperature is performed at ladle
treatment station.
Ladle
Furnace acts as a buffer between LD-Converter and continuous casting machine
and is used to :
-
-
adjust
the chemical composition (fine- tuning) of molten metal exactly as per required
steel grade.
- produce a wider range of steel grades.
- produce a wider range of steel grades.
-
de-sulphurise
steel.
-
hold
the molten steel for casting operation.
-
raise the temperature of steel (superheat) in ladle required to maintain
casting operation.
Experiencing
the use of cold tundish boards for continuous casting, introduced in 1986
stipulated to increase the tapping temperatures to an average of 15 0C
and after that induction of 6-strand Billet Caster from Voestalpine Austria in1989
further caused an increase of average tapping temperature to 300C,
required to compensate the need of superheat for prolonged casting duration of
steel for smaller sizes moulds of Billet caster.
In
the absence of Ladle furnace, the above modifications led to increase the overall
load of higher tapping temperatures on Converter refractory lining, increased
the holding time and confined the productivity of Converter.
Maintenance of LD-Converter to
prolong service life:
LD-Converter’s Mouth De-Skulling.
After processing a sequence of 12 –1 5 heats, the Converter’s mouth becomes dirty
due to slag and metal spatters and this skull build-up needs to be cleaned to maintain
the converter’s mouth workable for scrap
and hot metal charging.
As per project the mouth de-skulling
operation was carried out by hitting the deposited skull with specially
designed scrap box lifted with180 tons overhead charging crane which had been causing adverse impact on
the converter’s cone and liprings and lowered down the overall productivity of
Converter. Later in the year 1991, a refractory lining breaking machine was introduced which carries out
de-skulling of converter mouth without engaging overhead charging crane and
without imposing any adverse affect on structural integrity of Converter’s
components.
During
operation, the top refractory rings of converter mouth and subsequent layers
of cone bricks are subjected to severe
erosion of high velocity flue gases and come in contact with molten metal and
slag ejections. Excessive erosion in this area leads to collapse of top bricks
and subsequent refractory layers causes exposure of refractory retaining plates
and lip rings which could damage during mechanical de-skulling and put the
Converter out of production cycle. To prevent this mishap, the Converter’s
mouth is timely deskulled and mouth refractories are maintained by spraying
gunning mass regularly.
Failure
to remove skull buildup also adversely affects the center of gravity of the
Converter, causing unsafe operating conditions. If the skull buildup is not
removed timely, heavy deposition of metal and slag amalgam trapped in between
the edge and liprings requires time-consuming extensive cleaning which may lead
to delay the charging operation and hence leads to discontinue the production
cycle.
LD-Converter’s Refractory Maintenance.
The refractory lining of LD-Converter works
in severe conditions of high temperature and oxidizing atmosphere. After days of service,
the refractory bricks start getting worn out faster in some critical areas
of Converter lining due to heavy
corrosive attack of metal and slag to
the extent that timely hot repairs become indispensible to prevent premature
loss of entire refractory material of a converter’s lining campaign.
Gunning Maintenance:
As per project, the lining life was 300
heats. Later in 1984,
by modifying the Tar-dolomite lining scheme in cylindrical portion of Converter
and establishing the regime of Oxygen blowing, the lining life was enhanced to 350 - 400
heats per campaign (in
particular trunnions and slag line are very weak areas in the Converter).
Introduction
of Gunning maintenance in the year 1990, has led to a significant increase in lining life
of Converter, despite
simultaneous adverse affect of increased tapping temperatures due to use of
cold tundishes and Billet Caster without ladle furnace.
After
days of service when a lining wear of about 300 mm is observed on the trunnions,
slag line and upper cone, a scheduled gunning with MgO based refractory mass is
started to carry out on crumbling zones of the lining regularly (Pakistan
steel’s practice) which has enhanced the lining life to 500 – 550 heats and enhance the
availability of Converter for production to a reasonable extent under the
prevailing operating conditions discussed above.
The
gunning machine is comprised of a telescopic gunning lance that is mounted on a
Carcass frame with electric drive, a water pump, a material tank, water and
material hosepipes and a regulation valve for the remote-controlled adjustment
of MgO base gunning mass and amount of water. A gunning repair is a time
consuming operation and takes10- 12
minutes.
As gunning material has a cost, so the unit
price of gunning refractories should always be balanced with the cost of the
left over refractories to be used in a Converter’s lining campaign. Excessive
use of gunning material cannot be economical and increases cost per ton of
steel.
Slag Washing Maintenance:
Slagging
or slag washing maintenance is carried out frequently after tapping the steel
and leaving a portion of slag (congealed with dolomite) on the bottom of
converter. The vessel is rocked from one pad to another to coat a thin layer of
about 2 inches of conditioned slag. Slagging operation fills small holes /
cavities/ refractory wear developed on the charge pad, bottom and the tap pad
but cannot cover the wear of refractories on side walls/ trunnion and two third
of cone areas. Slagging maintenance takes 1- 2 minutes.
Slag Splashing Maintenance:
A
nitrogen blow slag splashing technique has been developed during past 20 years
to allow slag coating especially on side walls / trunnion areas and generally
the whole vessel and is currently employed in many countries where the
steelmaking shops are equipped with this facility.
Slag
splashing is carried out normally after steel tapping by retaining total or
part of the slag on the converter bottom which is blown via a supersonic jet of
nitrogen gas through the existing oxygen blowing lance. During slag splashing
the molten slag is splashed on the sidewalls, cone and all over converter
lining by regulating the blowing height and nitrogen flow rate. Any leftover
slag is discharged. The coated slag layer acts as a consumable refractory
lining which protects the erosion of Converter lining in subsequent heats.
In
order to implement slag splashing technique the following shop facilities need to be studied/ revisited as first step:
-
Supply
of additional amount of nitrogen gas at required pressure and pipeline from
Oxygen Plant, provision of switch over / regulating valves, nitrogen gas hoses/
flanges etc.
-
Bulk
material conveyors system and overhead storage bins for supplying Dolomitic
lime or raw Magnesia.
-
The
oxygen blowing lance and lance head configuration i.e. number of orifices/
nozzles, their angle of inclination to vertical axis of lance, diameter and
divergence angle of orifice to set flow of nitrogen jet on molten slag.
-
Normally
two oxygen blowing lance are provided to each of converter, one is working and
the other standby. Both of the lances are remained connected to Oxygen supply
line to overcome any failure during oxygen blowing. So time needed to switch
over from Oxygen to Nitrogen supply line should be taken into account during a
process cycle and should be added to the slag splashing total process time.
-
Slag
splashing frequency can be affected in a steel plant, producing steel grades
with varying chemical compositions from high carbon to low carbon grades.
Consequently the end point chemical composition, oxidation state, viscosity and end temperature of slag are wide-ranging and are changed with the steel grades produced.
Consequently the end point chemical composition, oxidation state, viscosity and end temperature of slag are wide-ranging and are changed with the steel grades produced.
-
Successful
implementation of slag splashing technique requires a slag with low FeO content
(around 10-13%) and high MgO content ( 11- 14 %),which is desirable to form
high melting material MgO.Fe2O3 in slag to coat on long life vessel’s lining.
Where as MgO > 10 % in slag prevents de-phosphorization and reduces yield. Also the iron content of the slag is a main source of iron loss.
Where as MgO > 10 % in slag prevents de-phosphorization and reduces yield. Also the iron content of the slag is a main source of iron loss.
-
As slag quality / properties
are of prime importance to achieve promising results of slag splashing, so a
compromising and most favorable composition of slag is required to satisfy the
needs of individual steel plant which could achieve optimal protection of
refractory lining without disturbing the production and operational goals.
-
A
highly viscous / sticky slag for splashing containing high melting constituents
has been reported to elevate the lance skull build up problem during slag splashing
requires frequent replacement of oxygen blowing lance. Heavy accumulation of
slag on oxygen lance tends to hinder the movement of lance through the lance
entrance / opening in converter hood or chocking of lance nozzle may force to
stop the converter production cycle.
-
Frequent
skull build up on bottom is also reported which tends to reduce the effective
volume of Converter and leads to upset the oxygen blowing height causes
slopping, loss of yield and increases erosion of mouth refractories. In order
to maintain proper blowing height, the bottom is usually flushed down which
hampers the productivity of Converter.
-
Also high production rate (e.g. when Converter
feeds bigger sizes of slab caster’s moulds) may hinder slag splashing
maintenance. As higher production rate means lesser time for preventive
repairs.
Slag
splashing technique is being employed in various steel plants world over to
increase refractory life of Converter. Increase in lining life depends on the
frequency of slag splashing which varies from plant to plant in accordance to
the prevailing technological parameters and operating conditions of individual
plant.
The optimal tapping duration:
The
purpose of the tap hole is to allow controlled tapping of steel only, leaving
the slag in the Converter and directing the metal spurt into the ladle.
De-oxidation and alloy additions are made to the ladle during tapping operation
to bring the raw steel to the required chemical composition.
As
per project refractory life of tap hole was as low as an average of 10 heats
and after that it was frequently repaired by re-piping with a shuttering of
steel pipe and filling MgO base mass for producing next 09-11 heats.
Later
in 1990, imported Isojet Tap hole Block
system ( pre-assembled MgO- C tap hole blocks) was introduced, comprised of dual-
ring tap hole assembly blocks system, in which the wear is retained within the
inner concentric ring thus permitting the outer ring to maintain the integrity
of the entire assembly. The inside refractory rings are changed upon wearing
normally after 100 heats. The Isojet taphole block system has significantly
improved the frequency of tap hole repairs and reduced down time.
The
tap hole is generally repaired when tap time reaches to three minutes. The
recommended tapping duration for 130 ton LD-Converter is between 3–7
minutes so as to attain optimal consumption of deoxidizers, consistency of
alloys recovery, steel quality and productivity of converter could be
maintained.
The
tap area refractories are eroded due to contact of molten metal and aggressive
slags. To maintain proper thickness of refractory lining in the tap area, the
gunning mass is sprayed regularly which prevents any metal breakthrough from
converter shell during tapping.
Prolonged
tap duration reduces productivity of converter, requires higher tap
temperatures which causes extensive wear of tap pad refractories and increases
thermal deformation of Converter’s cone and tap pad area (shorten vessel
life).
Shorter tapping duration than recommended restricts ladle
additions and de-oxidations, increases slag carryover in ladle results in
excessive burning of Ferro alloys, phosphorus reversion, retards desulfurization
and hence deteriorates quality of steel.
A rising demand of quality steel grades requires restraining
the amount of slag carry over to the ladle at the end of tapping. Various
measures are taken to prevent the final slag from flowing with metal into the
ladle during tapping such as throwing into the converter a ball-shaped device
or refractory cone- shaped plug called dart which is lighter than metal but
heavier than slag, it floats on the metal and closes the taphole at the end of
metal tapping.
Pakistan steel had tried the refractory ball slag stoppers
experimentally but their performance was found unsatisfactory. These stoppers
are not able to fully prevent the passage of slag but diminished the quantity
of slag in the ladle metal.
Under the prevailing operating conditions, Pakistan steel has
trained its steel tapping operators to handle the slag carryover problem
manually by using judgment skills of their eyeballs with particular emphasis on
keeping the tapping duration not less than three minutes and this practice
works as good as any refractory ball stopper without any investment.
In order to achieve close control of chemical composition of
hi-tech steel grades (e.g. automotive, oil/ gas pipeline, railroad steels) a
pneumatic device has come into use over last 20 years which is installed at the
tap hole on the outside shell of the vessel. An electromagnetic slag detector
actuates a stopper which pneumatically closes the taphole before commencement
of tapping and after all the steel is tapped.
However a sophisticated
device like above involves investment and it does not work stand-alone. It works
in steel plants facilitated with a computer controlled dynamic model for
converter operation that accurately controls the steel making process. (Turn
down chemical analysis, temperatures, slopping/ ejection out of converter).
Factors affect the Performance of
Refractory Lining.
-
The
quality of refractories employed and their maintenance.
-
Quality
of brick laying work.
-
Specific
volume of Converter which varies from plant to plant.
- Design of oxygen blowing
lance orifice tip.
Affect of Processing
Method:
a)
Higher
pressure of oxygen and height of oxygen blowing lance above the bath level reduce lining life.
b)
The
carbon content at the end of the blowing = <
0.03% , reduces lining life faster.
c)
The
metallic bath temperatures at the end of blowing >16700C, reduce
lining life faster.
d)
Higher content of Silicon in pig iron, reduces
basic lining life.
e)
The
CaO content in the soft burnt lime > 90% ,uphold basic lining life.
f)
Addition
of dolomitic lime in early slag to
saturate MgO content 7-8 %, prevents dissolution
of MgO from refractory bricks, uphold basic lining life.
g)
Properly
distributed and timely dosage of flux ( lime + dolomitic lime ) in accordance
with chemical analysis of metallic charge, uphold lining life.
h)
Growth
of aggressive oxide FeO in early slag is needed to dissolve lime but excessive formation of FeO in slag severely
reduces lining life of Converter.
i)
Careful
preparation and distribution of scrap in scrap charging boxes / trays such that
lighter scrap on face and recommended heavy / large sizes on back, reduces the
impact load of falling scrap on
refractory lining on charging pad, upholds lining life.
j) Excessive
amount of holding time of a heat in the vessel reduces lining life.
k) Minimize use of CaF2, uphold lining life.
l) A re-blow of 20
seconds consumes the refractory lining required for one heat.
k) Minimize use of CaF2, uphold lining life.
However the above suggestions
could be a guide line for ready reference but need separate comprehensive
enlightenment on each action.
.
Refractory
Lining of 130 ton LD-Converter:
The working lining of 130 Ton LD-Converter at
Pakistan Steel is comprised of Tar bounded dolomite bricks which are
manufactured in Lime & Refractories Production shop Pakistan Steel by
processing raw dolomite (CaCO3. MgCO3 ), available in the vicinity of Jhimpir district Thatta.
Removable Converter bottom:
The
LD-Converter of Pakistan Steel has a removable bottom. The bottom is fasten to
the converter with wedge lock plates by raising and clamping the bottom
underneath converter with the help of a specifically designed (Russian make)
hydraulic jack car.
As
per project three bottoms were made available such that two are attached with
two of each Converter in operation whereas the third one remains under relining
work at shop floor to get ready for use in the succeeding relining campaign.
The
converter bottom is lined with heavy duty Chrome- Magnesite XMKK bricks which
are stable bricks at high temperatures of steelmaking.
The
removable bottom facilitates quicker cooling, demolishing and removal of
discarded bricks and assists in relining work of LD-Converter.
However
there is always chance of metal penetration through the bottom joints during
production cycle if a thick layer of basic slag (congealed with MgO) is not
maintained over bottom bricks and sealing bricks joints.
The
converter bottom height with reference to Oxygen blowing lance height is measured
at least once a day to accomplish regime of oxygen blowing. Maintaining proper
height of converter bottom is necessary to obtain good yield, control of lining
wear, and reduce slopping and smooth converter operation.
Extensive
wearing of bottom refractories is observed during production of long series of
deep drawing steel grades ( carbon < 0.03%). During production process when
the bottom height can not be raised by normal slagging maintenance to the
required level, then it is repaired by leaving a mixture of liquid slag and
broken Tar- dolomite bricks on the bottom lining for at least four hours (current
practice at Pakistan Steel).
.
LD-Converter’s Cold Repair:
After
finishing a campaign life of refractories, the Converter is stopped for
demolishing the worn out refractories and to carry out relining work, known as Cold Repair.
Demolishing of Converter refractory lining after finishing campaign life.
After
finishing the life campaign, the converter is flushed out to remove Converter’s
bottom with the help of hydraulic jack car.
The
worn out working lining is cooled and demolished by using a lining breaking
machine shown above. The discarded refractory bricks are dispatched to slag
dumping yard for onward disposal.
The
Converter relining work is carried out with the help of a Telescopic hoist which
permits step by step elevation of foldable working platform entering from the
bottom hole into the upright positioned converter to support workmen and
refractory materials.
Simultaneously
during Cold repair, the broken equipments/ instruments pertaining to converter
operation are overhauled and any unbearable mechanical, electrical, Heat &
Power and automation fault revealed during preceding operational campaign is
rectified.
The
relining work (Cold Repair) takes 60-72 hours which considerably increases downtime
and labor cost.
Needs to use
refractory bricks with high performing characteristics.
Despite employing the above discussed
efforts, the lining life could be increased barely an
average of 550
heats per campaign
which is a bottleneck to the availability of Converter for production.
Achieving
high availability requires maximizing lining life and reducing the number of
reline campaigns. This could be achieved by improving
the quality of basic working refractory lining of Converter.
Magnesia-Carbon
Bricks.
In industrially
developed countries, large high density Magnesia-Carbon bricks of varying
chemical composition (Zoned lining) are used in steelmaking furnaces to
minimize down time and to achieve optimal pace of quality production.
Medium quality Magnesia- Carbon
bricks were tried by Pakistan Steel during 1990
– 93 in steel making LD-Converters, imported from four European
suppliers which lasted for an average campaign life of 850 heats per campaign (compared to local Tar
dolomite bricks an average of 550 heats/campaign)
but their higher cost made them uneconomical.
Zonal lining of
LD-Converter:
As
per the wear conditions of refractories during operation of LD-Converter, the
lining scheme is generally divided in following different zones.
Zonal lining scheme of LD-Converter.
The refractory wear pattern varies from
plant to plant as per prevailing conditions of converter operation practice.
Various qualities of MgO-C bricks are designed for different zones of
LD-Converter as per the data of lining wear pattern obtained from the user. Critical wear areas
(impact and tap pads, slag lines and trunnion areas) in Converter are zoned with
bricks of the highest quality.
Conclusion & Suggestions:
1)
In order to achieve a levelheaded
quality production requirements and minimize downtime, Pakistan steel needs to
enhance the life of working lining of LD-Converter to at least 2500- 3000 heats per campaign on precedence in first phase which can be
achieved by making use of superior quality locally available Magnesite mineral.
Without improving the life of basic working lining none of the above refractory
maintenance operation could effectively further increase lining life of Converter.
2)
However
slag splashing technique is being employed in various steel plants world over
to increase refractory life of Converter and is also an economical re-use of
Converter slag. The frequency of slag splashing varies from plant to plant and
depends on the prevailing technological parameters and operating conditions of
individual plant. Successful implementation of this technique needs to revisit
shop’s technological conditions, investment and necessary expertise briefly
discussed above.
3)
Subsequent to above up-gradation of
working lining of Converter, the service life of refractory lining can be further extended
to 5000 heats
per campaign or above by crafting an economical optimum balance of production, extent
of refractory maintenance, refractory costs without humiliating the life of vessel’s
components.
4)
None
availability of Ladle furnace facility in steelmaking department is one of the
bottlenecks, confining the productivity of LD-Converter. Provision of ladle furnace would eliminate un-necessary
thermal and processing burden of 15-20 minutes on the Converter’s refractories,
resolve quality issues, prevent any risk of returned heat from continuous
casting due to drop of temperature and put off delays/ discontinuing the
process cycle.
5)
After
tapping the steel from Converter, the need of vacuum degassing depends on the
objectives of production of quality steels of higher degree of cleanliness currently
required for manufacturing automotive grades (light weight high strength
steels), rail road steel, oil/gas pipeline grades etc. Vacuum degassing
involves exposing liquid steel to a low absolute vacuum to remove excess
hydrogen and to produce ultra low carbon and low sulphur steels. Induction of
RH type degasser in steel making department may be deemed at a later stage of
revamping.
No comments:
Post a Comment
Note: Only a member of this blog may post a comment.