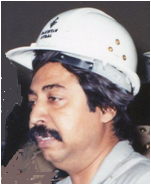

LD-Converter Slag Disposal Facilities
(Steel Making Department Pakistan Steel).
The
LD-Converter (BOF)
charge may consist of 10–25% of steel scrap and 75–90% of molten Pig iron. In order
to remove the unwanted chemical elements of the melt, the LD-Converter is
charged with fluxing agents, such as high calcium burnt lime (CaO), dolomitic lime
(MgCa(CO3)2) and fluorspar (CaF2), during the oxygen blowing cycles.
Carbon
dissolved in the molten Pig iron is oxidized to form carbon monoxide, causing
the temperature to rise to 1660–1710°C .The scrap is thereby melted, and the
carbon content of the molten iron is lowered, transforming it into raw steel. The
impurities combine with the burnt lime or dolomite forming liquid slag and
reducing the amount of undesirable substances in the melt. Resulting slag is a
major by-product of the steelmaking process floats on top of the molten steel because
of lower densities of slag constituents.
The
main chemical constituents of the LD Converter (B.O.F) slag are CaO, FeO, and
SiO2. During
the conversion of molten Pig iron into steel, a percentage of the iron (Fe) in
the hot metal cannot be recovered into the steel produced. Depending on the operating
practice of LD Converter, the chemical composition of resulting slag ranges as
follows,
CaO --------
45
– 55 wt.%
MgO --------
0.4
-- 4 wt. %
SiO2 --------
14
– 20 wt.%
MnO -------- 7 -- 14 wt.%
P2O5 --------
1-- 2 wt.%
Al2O3 --------
0.5
– 2 wt. %
FeO -------- 5 -- 11
wt.%
FeO/
Fe2O3 (Total) may range 20 –30 wt %
X-ray diffraction testing of LD- Converter slag samples have revealed
that the above chemical constituents are mostly present in the form of mineral
phases as merwinite (3CaO·MgO·2SiO2), olivine (2MgO·2FeO·SiO2), -C2S (2CaO·SiO2), (4CaO·Al2O3·FeO3), C2F (2CaO·Fe2O3), CaO (free lime),
MgO, FeO and C3S (3CaO·SiO2), and the RO phase (a solid solution of CaO-FeO-MnO-MgO).
Large
quantities of calcined lime and dolomite are used during the process of
conversion from Pig iron to steel and hence, the CaO content of LD Converter
slag is typically very high (CaO >45%) in order to keep the basicity ratio
higher (3 - 3.2). Although most of the lime exists in bound crystalline form with other
constituents in slag but the un-dissolved or free lime content can be as high
as 12wt%.
The
slag samples are concurrently taken with steel samples at the turndown of every
heat of LD-Converter subjected to regular auditing by Quality Assurance
Department and the analysis are regularly communicated to Steel production
manager so that corrective measures may be taken timely if required.
The
higher the percentage of impurities in the Pig iron, the higher the amount of
slag generated. The amount of slag generated per tonne of steel varies from
plant to plant, because of the difference in pig iron analysis, type and
quality of lime charged and the grades of steel produced. Normally an average
of 150 - 200 kg
of slag is generated per tonne of steel produced.
After
tapping each heat, Converter’s
slag is discharged into slag pot (mounted on a slag car positioned underneath
the converter ) through Converter’s mouth by rotating the vessel to the
charging side.
Above
is the view of LD-Converter floor (Pakistan Steel) at + 8 meter height and
ground floor beneath the LD-Converter, from where the electrically driven slag
car is operated (travels on conventional rails) to transport the Converter’s
slag to Slag dump yard of Steel Making Department.
Also
the slag resulting as by-product of deoxidation/alloying of steel in steel
ladles/ Ladle refining, is transported from continuous casting section via
general slag car to slag dumping yard. Presently three slag cars are employed
to fulfill the production requirement of 24 - 27 heats per day such that one
for disposal of Continuous Casting slag whereas other two for transportation of
slag from Steel Making Converters aisle.
To
meet the future requirement of expansion of Converter shop to 2.2 million tonne,
a provision of installation of third LD Converter and fourth slag car for
disposal of slag was left in the Soviet design.
Slag
is dumped from the slag pot by an overhead crane ( 30 tonne capacity ) into
slag pit of Slag dumping yard, located at the far end of LD Converter charging
aisle in the confines of Steel Making Department Pakistan Steel.
Generally
an efficient and economical design of the slag handling system is to utilize,
one slag pot per heat and turn-around time for one slag pot after cyclic process
of slag dumping, safety inspection, lime spray coating, putting down a
protective layer of dry slag at the bottom of slag pot and dispatching ready
slag pot for next heat, should be as short as fifteen to twenty minutes in
order to match the pace of peak production cycle.
Slag
dumping yard of steel making department Pakistan Steel is comprised of four
slag pits which remain in cyclic operation during peak production time such
that one pit undergoes slag pouring/dumping operation, second under water spraying/cooling,
third under slag removal/ disposal and fourth standby/ ready.
A slag pit is crammed after dumping slag of 50 - 60 heats, then it is stopped and slag is allowed to cool by water sprayers/ air. Subsequently the cooling slag is dragged and muddled, to allow further solidification of underneath layers of hot slag to turn into crystalline material and to get the slag pit completely dried.
Pouring of molten slag ( at 16000C ) on some left over excessive water in the slag pit may cause severe explosion and heavy slag splash out which can endanger the life of overhead crane operator and the people working around. It takes about 48 hours to get ready a slag pit to start next dumping operation. The method of water or air cooling employed effects the quality of slag obtained.
Disposal of Converter’s slag from slag yard Steel Making
Department.
All
above earth moving machinery used in slag handling at steelmaking department is
deployed and managed by Process Auto Transport ( PAT) Department of Pakistan
Steel.
The
crystallized slag is loaded through excavating shovels and trucked away via
haul trucks to slag granulation and metal reclamation plant.
At
metal reclamation plant, metallics are recovered from the slag by magnetic
separation. After removing the larger pieces of metal in the primary magnetic
separator, the slag is put through a classifier, then crusher, after which the
fine metallics are removed in secondary magnetic separator. The metallics are
returned for recycling in steel making and metallic- free slag is sized and processed
to make it salable in market.
Since
large quantities of lime is used in LD-steelmaking and most of the CaO exists
in bound crystalline form with other constituents in slag but LD slag can also
contain pockets of free lime (CaO). This free lime can absorb water to form
hydrated lime Ca(OH) which expands and
swell, making the LD slag volumetrically unstable overtime. So a better
understanding of the properties of steel slag is required for large volumes of
this material to be utilized in a technically sound manner in civil engineering
applications, mainly for road construction.
Industrially
developed countries have found various ways of utilizing it. The UK, US and New
Zealand use slag as aggregates in road construction, while Canada uses it as
railway ballast. In China, a type of composite cement consisting of a mixture
of LD slag and Granulated Blast Furnace Slag (GBFS) is used.